- HOME
- Products & Services
- Casting and Metal Machining (CMR)
Casting and Metal Machining (CMR)
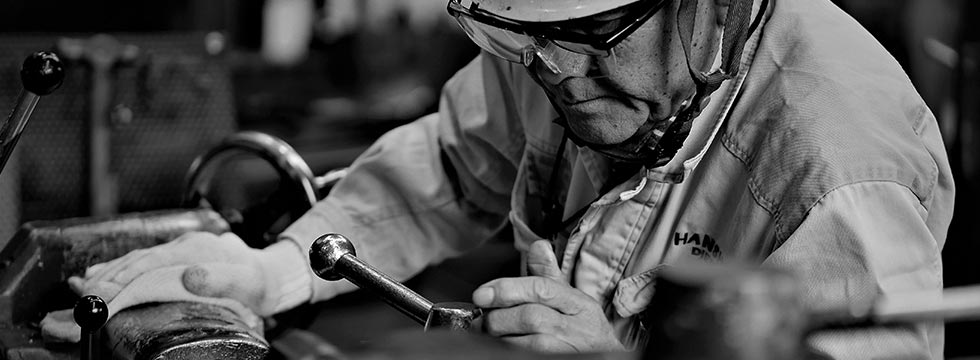
Our history in manufacturing that exceeds 100 years is not limited only to engines for vessels.
With our strong desire to spread the use of various technology and equipment and make contributions to manufacturing in Japan, we are continuing to carry out activities that provide customers with our technology and skill in the form of products.
-
What does
CMR stand for?It represents the three pillars of our technology: Casting, Machinery, and Repair.
Technology TECHNOLOGY
Masterful skill
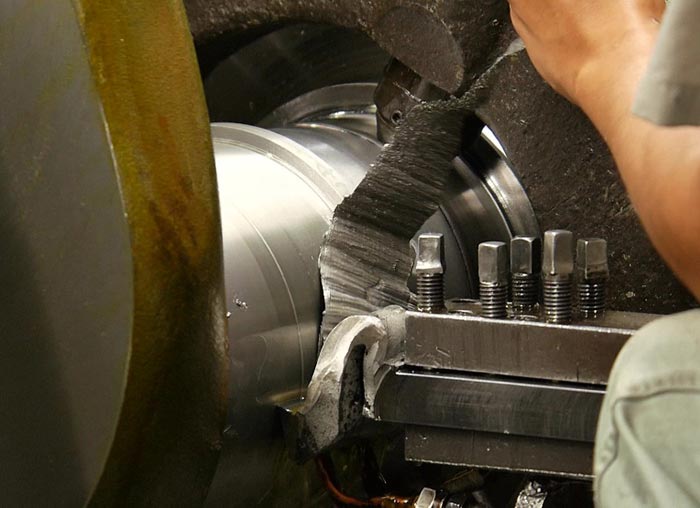
Spring-neck finishing
Finishes produced by using spring-necked turning tools are part of Hanshin's unique identity. Roundness achieved through machining at low revolution speeds is comparable to that of grinding, and is capable of approaches with a depth not possible for grinding machines. Processes that reach the ultimate level of performance while confirming chip thicknesses of 0.01 mm or less are true examples of masterful craftsmanship.
- Existing products that have been damaged can also be repaired.
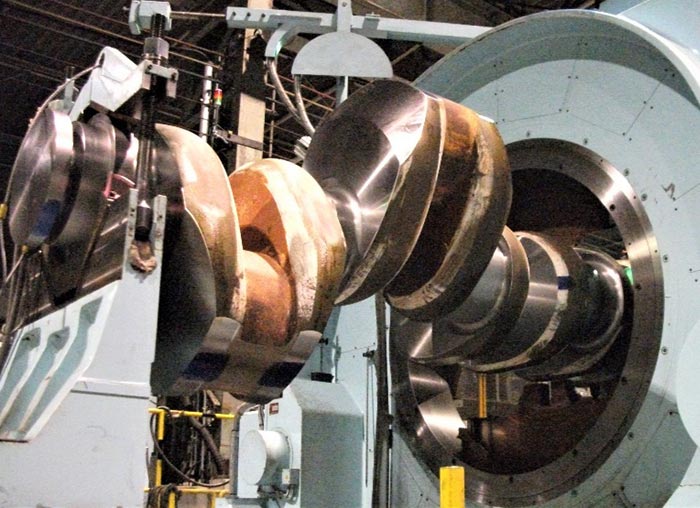
Eccentric shaft machining
In this type of machining, the workpiece is fixed in place and the machine itself turns. This machine has a structure which is the opposite of conventional lathes, making it an essential tool for machining large crankshafts. Its simple and unique configuration has a wide variety of applications, and can be used in eccentric shaft machining for industrial machinery including press machines and gas compressors. Including a spring-neck finish can achieve precision which is equivalent to or higher than that of grinding machines.
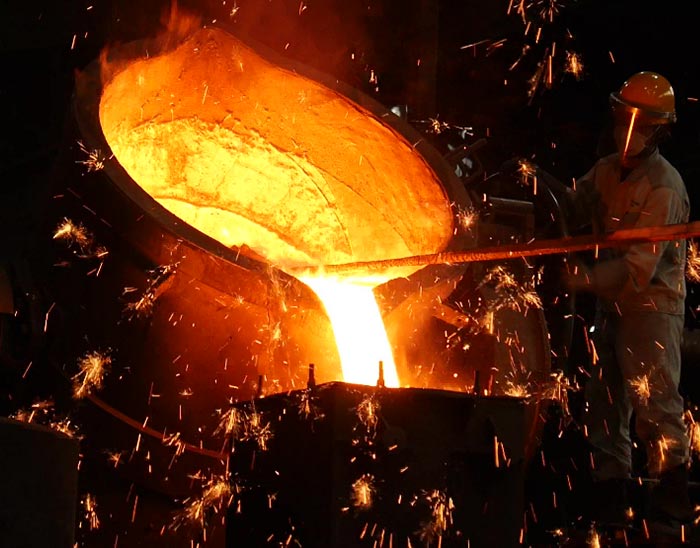
Casting
Technology in which iron at a temperature exceeding 1,300℃ is poured into a mold and formed into shapes is an ancient process that has been in continued use since prehistoric times. Even today, it holds a place as the foundation of manufacturing, and is continuing to evolve. In addition to products for vessels, Hanshin supplies products for machine tools, machine jigs, and other applications. We are also highly proficient in the integrated production of tube shapes (up to 5 m). Furthermore, we have begun the use of 3D modeling technology and reverse engineering, as we expand the fields of our activity.
Advancement
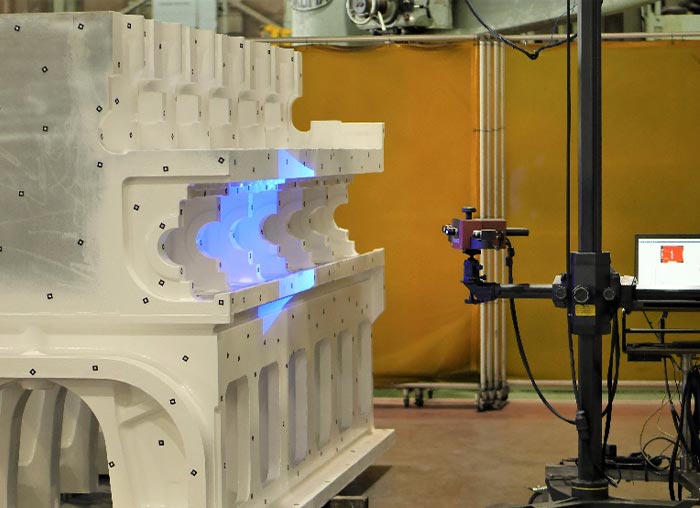
3D digital technology
We have incorporated 3D machining and 3D inspection technology into our production lines, and made extensive improvements. Cast product inspections which use 3D scanners can discover shape defects which could not be perceived visually in the past, and can assist in the elimination of marking work. We will continue to accumulate technology such as this to support operations for manufacturing.
Introduction movie
Machining of crankshafts for vessel engines
Equipment
-
-
Crankshaft lathes: 5 units (2 NC machines)
- Maximum workpiece size
- Swing: Φ2,100 mm × Center-to-center distance: 8,000 mm, Weight: 20 t
- Main machining examples
- Various eccentric shafts such as crankshafts
- Rotor shafts for generators
- Roll pins
- Press machine crankshafts
-
-
Crankshaft lathes: 5 units (2 NC machines)
-
-
Crank pin lathes: 5 units (1 NC machine)
- Maximum workpiece size
- Turning diameter: Φ1,400 mm
- Main machining examples
- Various eccentric shafts such as crankshafts
- Press machine crankshafts
-
-
Crank pin lathes: 5 units (1 NC machine)
-
-
NC 5-face machining equipment: 5 units
- Maximum workpiece size
- Width: 3,100 mm × Length: 9,000 mm × Height: 4,190 mm, Weight: 75 t
- Main machining examples
- General structural components for marine engines (cylinder frames, etc.)
- Large parts for machine tools
- Structures for industrial machinery, etc.
-
-
NC 5-face machining equipment: 5 units
-
-
Long lathes: 4 units (2 NC machines)
- Maximum workpiece size
- Φ1,400 mm × Center-to-center distance: 11,000 mm
- Main machining examples
- General stern shafts for vessels, such as propeller shafts
- Camshafts
- Rotor shafts
-
-
Long lathes: 4 units (2 NC machines)
-
-
NC machining centers: 13 units
- Maximum table size
- 1,000 mm × 1,000 mm
Maximum load capacity: 2 t
- Main machining examples
- Cylinder covers
- Cylinder liners
- Connecting rods
-
-
NC machining centers: 13 units
-
-
NC lathes: 13 units, NC vertical lathes: 4 units
- Maximum workpiece size
- Φ1,300 × Center-to-center distance: 3,000 mm
- Main machining examples
- Connecting rods
- Cylinder liners
- Piston crowns, piston skirts
-
-
NC lathes: 13 units, NC vertical lathes: 4 units
-
-
NC horizontal boring machines: 3 units
- Maximum workpiece size
- Width: 6,000 mm × Length: 1,300 mm × Height: 2,500 mm, Weight: 50 t
- Main machining examples
- General structural components for marine engines (cylinder frames, etc.)
- Large parts for machine tools
- Structures for industrial machinery, etc.
-
-
NC horizontal boring machines: 3 units
-
-
3D scanner
- We have introduced a 3D scanner produced by ATOS, which provides comprehensive support from machining to measurement.
- Area of 3D scanner measurement location
- 7.5 m × 8.5 m
- 3D scanner range of
movement - Radius 6 m × 180 degrees
-
-
3D scanner
-
-
Cranes
- Akashi Factory
- Maximum rated load: 75 t
- Harima Factory
- Maximum rated load: 200 t
At the Harima Factory, a 200-t crane is used for operations including marine transshipment from vessels to barges.
- Quay wall
- 499G/T pier landing is possible
-
-
Cranes
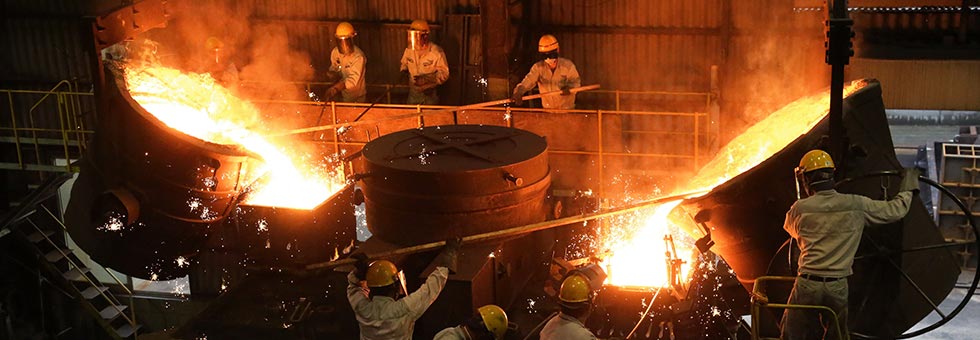
Casting
Melting equipment | Medium frequency induction furnaces | 6 tons/B × 2 units |
---|---|---|
High frequency induction furnaces | 1.5 tons/B | |
Analysis equipment | Pre-furnace analysis equipment (CE meter) |
2 units |
Sand treatment equipment | Furan self-hardening sand regeneration equipment | 10 tons/h |
Reclamation sand storage equipment | 200 tons | |
Sand cooler | 20℃±2℃ 20 tons/h | |
Post-processing equipment | Core knockout machine | 30 tons |
Monorail shot blasting | 2.8 tons | |
Other | Gas annealing furnace | Max. 3 tons |
Track scale | 25 tons | |
Production capacity | FC 200–350 | 15 tons (weight of as-cast materials) |
FCD 400–600 | 11 tons (〃) |
Consignment examples CASE
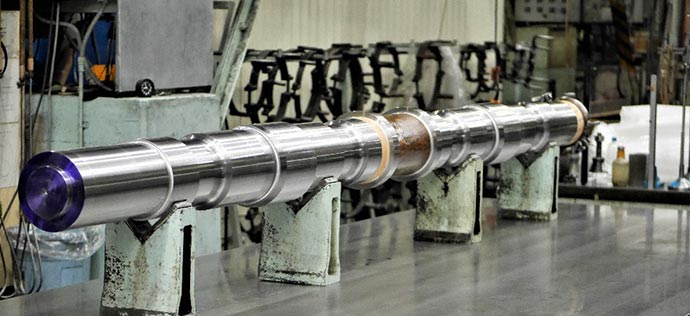
High-precision eccentric shafts for precision press machines
- Related equipment
- crankshaft lathes, crank pin lathes
Main components of precision press machines. Our expertise in crank pin lathes is applied in order to align the phase differences of eccentric shafts to the greatest extent possible. Requirements for precision can be met to an unmatched level.
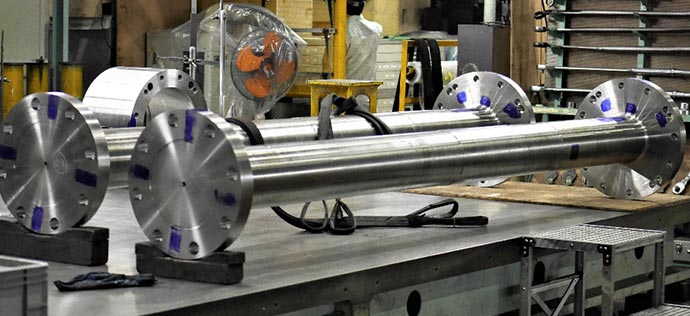
Stern interim shafts for vessels
- Related equipment
- long lathes, 5-face machining equipment
In addition to our own company's work, we also carry out contracted machining of stern-related components using long lathes. One strength of Hanshin is our ability to provide support even for ship classification society surveys.
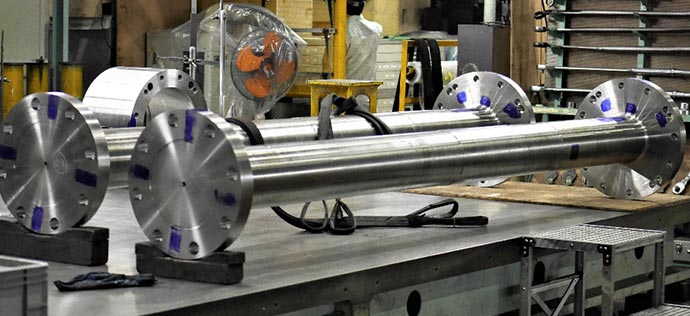
Crankshafts for presses (repair)
- Related equipment
- Crankshaft lathes, crank pin lathes
Repair of shaft-related parts that have worn down from many years of use can be entrusted to Hanshin. We will hold thorough discussions on the methods of repair with users, to provide quality that perfectly matches their requirements.

Gas engine frames
- Related equipment
- 5-face machining equipment
Our main 5-face machining equipment is outfitted with various types of attachments suitable for complex machining of engines for vessels. By centralizing work that had been performed by other processes onto a single machine, quality can be improved and delivery times shortened.
Delivery records
- AIDA ENGINEERING, LTD.
- Okamoto Co., Ltd.
- Kobe Steel, Ltd.
- KISHIRO TRADING CO.,LTD
- Kawasaki Heavy Industries, Ltd.
- NIPPON STEEL CORPORATION
- MITSUI MEEHANITE METAL CO.,LTD.
- DAIHATSU DIESEL MFG.CO.,LTD
- TanakaKogyo Co. Ltd.
- TECHNO TRY CO.
- DAITOKU KIKOU CO.,LTD.
- Manyo Co., Ltd.
- Sanyo Special Steel Co., Ltd.
- Hakuro Machinery Co., Ltd.
- NISHISHIBA ELECTRIC CO., LTD.
- Tamaki Ironworks Co., Ltd.
For questions, consultations, etc. regarding work requests
Please feel free to inquire with us.
- 078-923-3449
- 078-923-1121